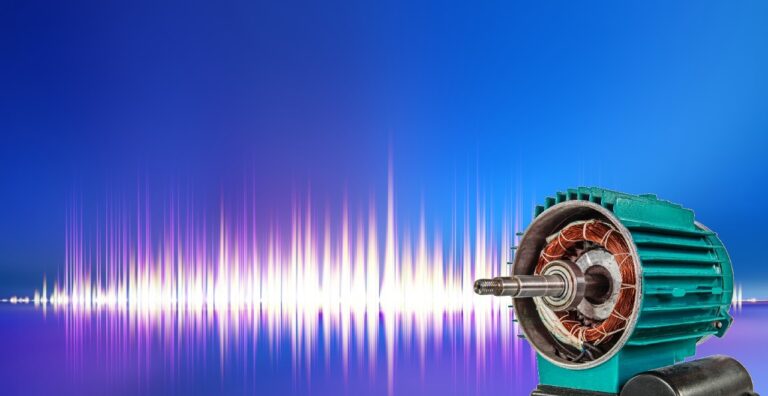
What you should know about Vibration Measurements
Any kind of rotating or oscillating equipment can be subject to issues that will manifest themselves early on through changes in the vibration patterns of your equipment. In order to catch these issues before they become a much larger issue, vibration monitoring should become a part of your predictive maintenance schedule. There are many different methods of interpreting data collected from vibration analysis, and in this article we will go over a few of the most common ones.
Overall Level
The overall level vibration check gives you a very limited analysis of the vibration patterns of your machine at any given time. Most technicians have strayed away from this method for more detailed methods of analysis. This method is used for getting a quick check of vibration levels, with the same amount of information generated as monitoring your equipment by feeling it with your hand. This method is best for a quick initial check on rotary machines, especially those running at high speeds.
Spectral Analysis
This method of vibration measurement transforms the signal from the time domain to the frequency domain using the Fast Fourier Transform (FFT) algorithm. The signal is then analyzed by a qualified technician to determine if there are any spikes in vibration frequency coming from any certain part of the machine and what issues this frequency would indicate. The peaks in these frequencies will give your technician clues as to where in your machinery the harmful vibration may be coming from. This method is usually used when the rotational speed of a shaft, or how often tooth meshing occurs, comes into question.
To perform spectral analysis, you need to conduct baseline testing on your application when it is first installed so you have information to refer back to at periodic testing intervals. You will also need to collect some additional information at the time of measurement. This includes: identifying all components of your machine that could be causing the vibration, identifying the machines running speed, as well as the running speeds of any adjacent machines (in case they are influencing the vibration patterns of the machine in question), finding out how the motor is mounted, and if it is overhung, or if it is connected to anything that is overhung. Then you will need to obtain any historical machinery data you have on hand and compare it to the recently acquired data and analyze the vibration patterns for any harmful trends.
Signal Averaging
This method determines the level of the signal at each individual frequency. It is most important for low frequency measurements, because of the extended amount of averaging time needed to get accurate data. This method is used in the monitoring of a single gear in relation to its rotational speed. Signal averaging can show you the cyclical action of each tooth in the gear being monitored. If one of the teeth has a large crack, it would easily be detected due to its increased flexibility and the change in vibration frequency that would occur.
Shock Pulse Monitoring
This method of vibration monitoring is a great addition to your predictive maintenance schedule. This method entails using a hand held device that gives off a natural frequency, that when applied to your equipment, is excited by shocks generated by damaged roller bearings. This method shows you when two pieces of metal touch each other while in motion. This contacting of metals will create shock waves that will develop from the impact, travel through the metal of the bearings and machine, and be picked up by the hand held instrument. These shock waves will then be analyzed by a qualified technician to look for any degradation in your roller bearings or their lubricant that could be causing unwanted vibration.
Kurtosis Measurement
Kurtosis measurement gives us an idea of the “spikedness” of a random signal. Signals that have a higher kurtosis value will have many peaks that are greater than three times the signal’s root-mean-square (RMS) value. This method has proven very effective at monitoring for bearing faults, but is not yet commonplace, although it is slowly headed in that direction.
Discrete Frequency Monitoring
This method monitors the vibration levels at a particular frequency against the levels we would expect that particular component to generate. (These frequencies are held in databases put together by vibration monitoring companies and have become extremely accurate over time.) As an example, if you wanted to look into a certain shaft in a machine, you would tune the monitoring system to that machine’s rotational speed and compare your readings to the frequencies in the aforementioned database. Discrete frequency is also calculated using the FFT algorithm.
Cepstrum Analysis
This method was originally used to measure seismic echoes produced by earthquakes or explosions. Cepstrum is used to look at repeated patterns in a spectrum. Repeated patterns in a spectrum are sensed as one or two components in the cepstrum with multiple sets of sidebands, like the way the spectrum separates repetitive time patterns in the waveform. This method of analysis is used to look at interactions between the rotational frequency of bladed rotors and the blade passing frequency. You can also use it to examine gear tooth meshing frequency and gear rotational speeds.
Each method of vibration analysis has its pros and cons. Getting in touch with a vibration analysis expert can help you decide which form of analysis is right for you and your application.
Got More Motor Questions? We Can Help!
Call 800-595-5315 Or Connect With Our Expert Technicians Here:
Other Articles
- How to Reduce Motor Downtime and Keep Your Motor Happy
- Critical Spare Planning
- The Three Most Common Externally Caused Motor Failures

Craig is the Vice President of Engineering at Energy Management Corporation. He is a Professional Engineer (PE) and carries over 30 years of experience in the world of electrical automation. Besides amassing an impressive amount of knowledge in his magnificent brain, he is also a Master Scuba Diver (MSD), a performing magician, and a professional DJ. Truly a man of many talents.