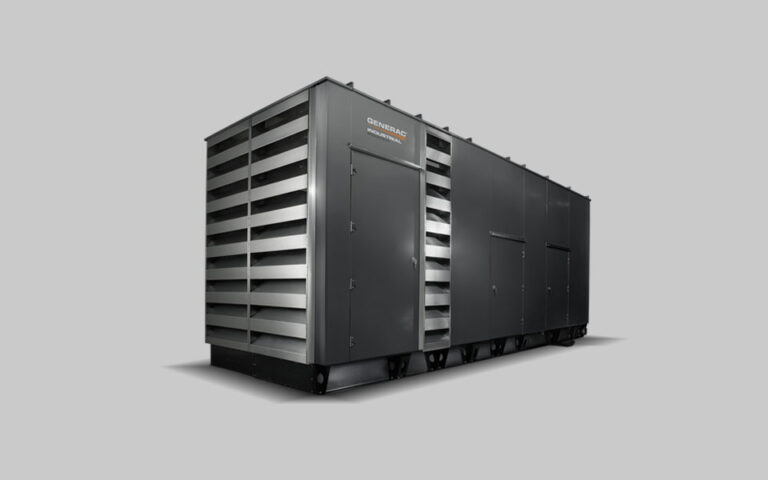
What are ways to increase the standby generator’s reliability?
Standby generators are usually installed in case of a power outage or emergency. What happens when an outage occurs and your generator fails to start? Did you know the number one reason for gen failure is a problem with the batteries? Let’s take a look at a few things you can do to improve your gens reliability.
Reliability and MTBF
The Nuclear Regulatory Commission states that “The reliability of diesel generators is strongly dependent on the interaction of the following factors: design, testing and operational requirements, operational history, inspections, maintenance, and the personnel qualifications of operators” (NRC Docket Nos 50-443/444). 95% of all generator failure can be prevented by proper maintenance. Generator reliability is measured by Mean Time Between Failure (MTBF). This is the amount of time between system breakdowns, or a failure to start. The longer the MTBF is, the more likely your generator is to start in the event of an emergency.
Location
Keeping your gen indoors creates a more controlled environment; it keeps the generator warmer and has less of a chance of developing corrosion. Keeping it indoors also allows the gen to be visually inspected more often as you walk past it and look at it. However, indoor gens can decrease reliability by requiring complex supporting systems, which could lead to more system installation compromises or oversights. They are also more prone to being damaged in a structure fire or being turned off or messed with by someone just passing by.
Outdoor generators increase reliability by using complete original equipment manager (OEM) systems straight from the factory. There is no need for complex aftermarket supporting systems. Keeping your gen outside also helps with issues pertaining to fuel piping, exhaust piping, air flow, isolation in case of fire, and limited accessibility by humans. However, the outdoors is a less controlled environment which leaves your generator susceptible to corrosion and cold temperatures.
Multiple Generator Solutions
The most reliable way to make sure your generator will start is to get a backup generator to your backup generator. Paralleling 2+ generators gives you 99.99% + reliability, up from 98% with just one. Paralleling generators can be a complex process, but this complexity can be solved with integrating the paralleling controls directly into one of the generators and using all digital controls and communications for interconnection. You can also mount the paralleling switch directly onto the gen, which optimizes your setup for reliable switching.
Serial Components
It is said that “The reliability of a series system is always lower than the reliability of any of its components”. Integrating control functions, fuel systems, exhaust systems, cooling systems and starting systems to be less complex is a great way to improve your reliability. Using a factory complete system is an easy way to do this. If you know that all the parts are designed specifically to be used together, there is less of a possibility of a problem.
Starting Systems
If your generator can’t start, the rest of the systems have no opportunity to fail. Your starting system should be one of the most well designed and maintained parts of your generator. The number one reason for generator failure is a problem with the battery. Poorly maintained connections, bad chargers, corrosion, poor alternators, and faulty starter solenoids are common areas of gen failure to start (FTS). Ways to mitigate some of these issues are through battery heaters and using high quality lead acid batteries that are properly maintained.
Engines
OEMS must invest heavily into their engines. You need to be sure that the gen you are purchasing comes from a reputable company that chooses the best engines from the best manufacturers. The engine needs to be optimized for standby generation. And although engines are very rarely the cause of generator failure, your engine should be maintained with regular fluid and filter changes, visual checks, operation checks, weekly no load tests, monthly load tests, and periodic load tests at full load. All of these should be done by certified dealer technicians for the best results.
Alternators
Generally speaking, alternators are quite reliable. To get the most from your alternator you need to be sure it is getting cooling air while avoiding recirculation and intake debris. The load also must be balanced. Setting procedures to check load balance regularly can be helpful to not overload a specific coil group.
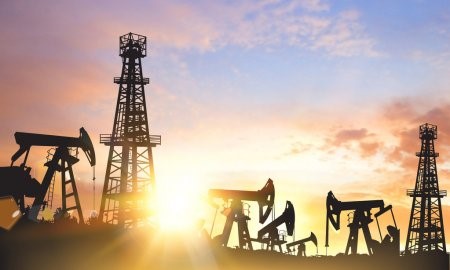
Fuel Systems
Trouble with fuel systems is the 2nd most common reason for gen failure, behind problems with the starting system. Dirty fuel filters are a major cause of generator failure or reduced load capacity.
For compression ignited fuels like diesel, maintenance of fuel is critical. Moisture, gelling, biomass, and fuel instability are all concerns with the newer generations of low-sulfur diesel fuel available. A diesel fuel service maintenance program is required to combat these problems. Storage of fuel is an important component to your maintenance program. Sub base fuel tanks are a cheap and simple way to store fuel and keep sludge from building up with a slanted bottom for collection. Day tanks with a main storage tank are great for preventing fuel spills and providing a reliable supply of fuel.
For spark ignited fuels like natural gas (NG), LP vapor, LP liquid or dual fuel (NG and LP) you don’t have much maintenance of fuel to worry about. The main concern is interruption of supply from utility, and this is something out of your control.
Bi fuel systems can greatly increase reliability. While diesel is the igniter, 75% of the energy produced comes from the natural gas supply. This extends operation time while minimizing on-site fuel. Bi fuel gens can also run 100% on diesel if NG supply is interrupted. (This does not work inversely.)
Cooling
On gen closed cooling systems are the most reliable. Off engine systems like remote radiators, heat exchangers, circulation pumps, and cooling fans are the least reliable. This is because of the added parts and as discussed above, more parts = more areas for failure.
Air Flow
Some ways to increase air flow are to make sure your exhaust discharge is a short straight run (size should match the radiator opening), with a typically .5 to 1 inch water column back pressure. Your exhaust inlet should have an area 1.5 to 2 times the size of the radiator opening with no air handler for best results.
Controls
Controls are a major reason for gen failure if periodic maintenance is being done at a high level; techs sometimes forget to just turn it back on! 20 – 40% of all failures are related to controls. The more integrated your controls are, the better, as there is less room for operator error. Some other common solutions to control problems can be found in the table below:
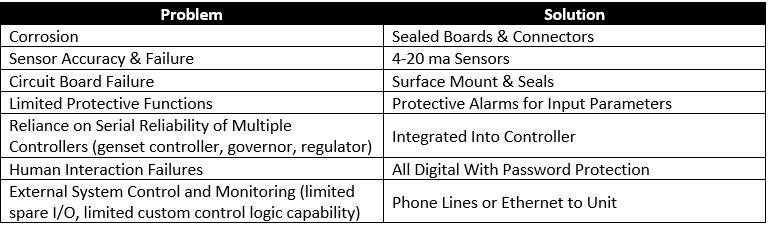
Turn it Back On
But what if you are maintaining your gen meticulously and have all the correct equipment and it still won’t start? Make sure it is turned on and not displaying the error message “Not in Auto”. If you see this message, this means that somewhere along the way, someone turned off auto mode for maintenance and never turned it back on, causing your gen to fail to start when you need it most.
Got More Generator Questions? We Can Help!
Call 800-595-5315 Or Connect With Our Expert Technicians Here:
Other Articles
- Critical Spare Planning
- Where Do I Start On My Generator Installation?
- How can Las Vegas heat lead to generator failures?

Craig is the Vice President of Engineering at Energy Management Corporation. He is a Professional Engineer (PE) and carries over 30 years of experience in the world of electrical automation. Besides amassing an impressive amount of knowledge in his magnificent brain, he is also a Master Scuba Diver (MSD), a performing magician, and a professional DJ. Truly a man of many talents.