Don’t Get Caught in Unplanned Downtime; Plan Ahead with Critical Spares
Downtime is one of the biggest issues that many on-site engineers, supervisors, and managers dread. Whether you’re a manufacturing facility, an extraction site, a packaging company, or a utility provider, downtime means lost production, lowered revenue, and high costs.
When there is an unexpected failure, you not only have to pay wages and expenses while you’re down, but you may be looking at overtime for your employees or contractors to get you back up and running.
Every minute counts. Having a critical spare plan means that extra equipment is nearby that’s ready to swap out and reduce your downtime. At the same time, having too many spares means you have over-invested in equipment and have increased upkeep expenses.
How do you ensure you have the exact spare equipment and that it’s ready when needed? We’ve dealt with emergency electrical retrofits for decades, especially around aging infrastructure. We’ve seen that several best practices for your critical spare plan can help lower costs, reduce downtime, and prepare you for the next emergency.
How do I identify critical processes and components?
The first step to any critical spare planning process is to identify what spares you need to have ready and what you can go without. This process involves looking at your electrical system, determining the value of the spare to your process, and identifying possible failure points.
Determine critical electrical system components
One of the best places to start is to pull out your most recent electrical one-line drawings. If you need up-to-date drawings, you likely need to look into a service to do that and go through an arc flash study.
Need up-to-date drawings or studies?
EMC can perform an arc flash study and help update your electrical drawings drawings.
Looking at your one-line can help you identify points in your system with equipment that could be a lynchpin. If all electricity for your critical processes flows through one set of equipment, it’s worth identifying whether it’s worth stocking spares for.
It would be best to also look at the production flow and processes. A manufacturing facility may have five production lines but they’re all fed by one conveyor belt. In that case, a failure on your conveyor means all production lines go down. Look for critical processes that would have an outsized impact.
These critical processes often include transition points from one process to another. That may be a conveyor, a compressor, a pump, or something similar.
Also, identify equipment that may be important for some other reason. Is it proprietary equipment that is important to have running? Is it essential for life safety, such as a generator for emergency lighting or fans for proper ventilation in a mine?
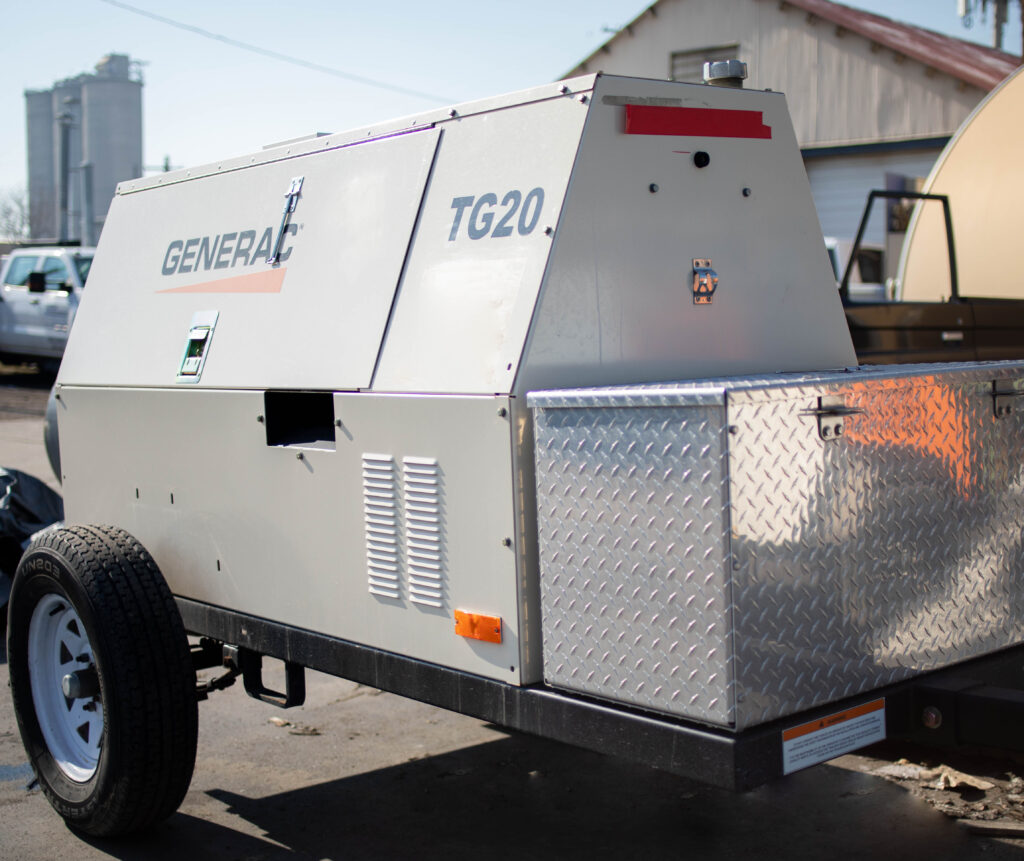
Identify the value of spare availability
While you’re looking at lynchpins that could bring your process down, look at areas that could cause the highest loss of revenue or emergency repair costs.
You may have a particular piece of equipment that produces the highest product output or the most valuable components. While that equipment failing may bring down relatively little of the whole system, you will still lose extra money on revenue.
One common issue is that last-minute replacements often lead to high logistical costs. You may have a massive motor and the logistics of moving the motor in a rush means extra crane charges, trucking expenses, or other issues. Identifying custom or large equipment that gets exponentially more expensive in an emergency helps you know that you should keep those products closer to hand.
Some equipment may also take a lot of labor that is expensive to have wasted. You may see that certain equipment runs automatically while another piece of equipment takes three technicians to operate. In case of failure, you now have underutilized labor to account for as a cost.
Find likely failures
The frequency of failures is the last piece to look at. Even if the equipment is less valuable to your process or hard to replace, you can see downtime start to add up if it fails often.
It may often fail due to factors internal to your facility. Does your facility have a demanding environment, such as being dirty or humid? Does it have extreme temperatures? Does it have bad power quality, such as harmonic issues, surges and transients, or power factor issues?
You may also have processes that cause premature failures. For example, we’ve seen that motors close to crushers may fail prematurely due to excessive vibration, which can cause bearing damage. How you use or maintain the equipment could also affect its lifespan, such as whether you maintain it properly or tend to run it with excessive starts and stops or use high overloads.
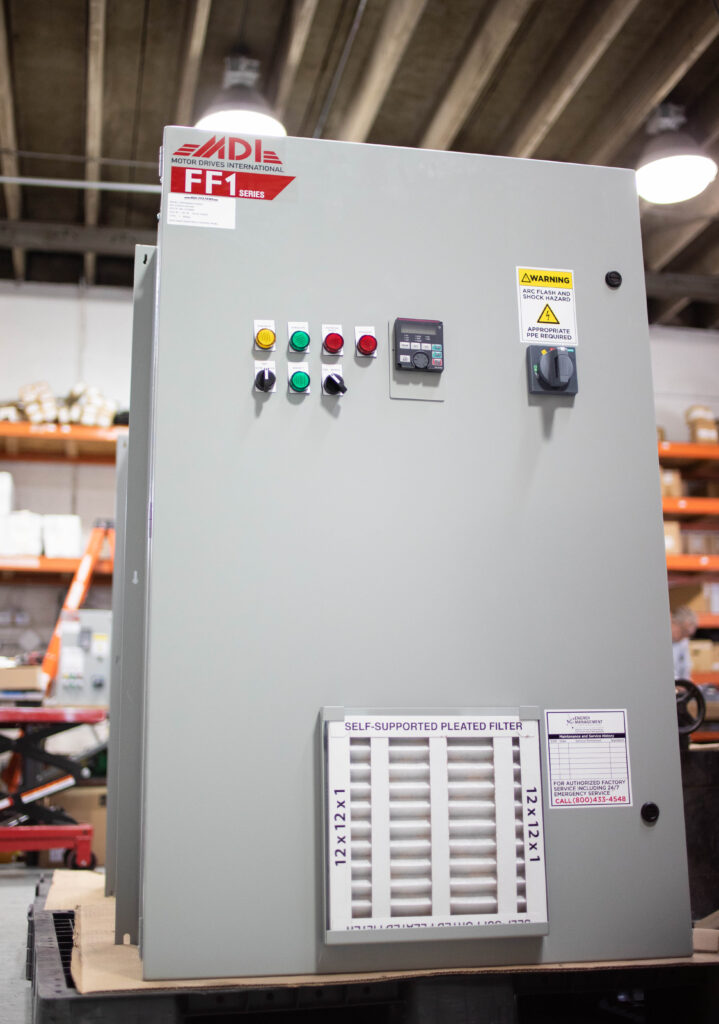
External factors can also affect your equipment. You may be in a part of the world that is always hot, cold, humid, or dirty. You may have many surges/transients, harmonics, or other issues with your utility power. The demand in your market or industry could mean that your plant and equipment has to operate harder or longer than it was initially designed for.
We often see that aging infrastructure is a problem with repeated failures. As electrical equipment ages, it may have components fail more often. A generator may have more engine failures, a VFD may have cooling system fans go out, or motors may start seeing more bearing failures. These failures can often result from aging equipment being subject to strenuous or repetitive use.
How should I source spares?
Once you’ve gone through the process above to identify which equipment may be critical to you, you can begin sourcing the spares to have ready for those processes. This process will involve looking at lead times, market conditions, logistics of delivery, and warranties.
Identify lead times options
Replacing equipment is one of many options when you have a failure. You may consider major repairs or even take the equipment out of service for reconditioning to avoid emergency failures. In these cases, you need to consider lead time for repair or reconditioning.
We’ve seen that recent lead times mean that you need to re-examine many prior assumptions. A new motor may take a year to arrive, whereas a significant repair or recondition may take a few months. Many processes can’t afford to be down that long, so having a spare to put in place in case of failure will give you time to order new or repair the existing equipment.
As you look at this, realize that you might not always be able to order a drop-in replacement, which may affect your timeline. If equipment is obsolete, you may see different brands, new dimensional layouts, the need for a mounting base or enclosure, conduit and wiring adjustments, or other issues. These adders may increase the lead time of the whole system.
Need a Backup?
Let EMC’s experts find you the spare that you need.
Evaluate market and supply chain conditions
More than ever, facilities are seeing that forces outside their control are affecting lead times and availability of equipment. VFDs, motors, generators, and many other products have seen widely fluctuating production and delivery times based on shortages of parts and labor.
When you’ve identified the spares critical to your site, identify the internal components to that equipment and which of those may have issues availability issues. It may be processor chip shortagesor raw steel material issues, but as part of your sourcing plan you should consider these issues.
Identify shipping issues
Shipping and logistics issues seem to be at an all-time high. To source products, we’ve seen an increase in international, large, and custom deliveries. Many facilities are having their first encounters with custom packaging, hotshot deliveries, or oversized load considerations. You should consider these issues and how they impact lead times and cost.
We’ve also seen that cranes for offloading equipment at the site have delayed availability. Many sites are looking at getting spare parts on site or to a local vendor early and holding them where it’s easily accessible in case of emergency.
Consider warranties
As spares are brought in and stored, the warranty for the equipment is something to consider. Some brands have strict policies that the warranty starts at production or shipment, while others will allow a six-month delay before the warranty begins if you haven’t installed the equipment yet. Although you hope to never use a warranty, it’s important to identify what warranty you’ll receive before you order spares.
How do I store and manage spares?
Once you have your spares on order, you need to make sure you have a plan for storing and managing them, including where you’ll keep your spares, how you’ll maintain them, how you’ll manage your inventory, and what reports and trending you can do for improvement.
Choosing a storage location
The location of where you will store your spares is essential to make sure the money you invested doesn’t go to waste. Some facilities keep spares with a vendor or contractor, while others store them at their own production facility or warehouse.
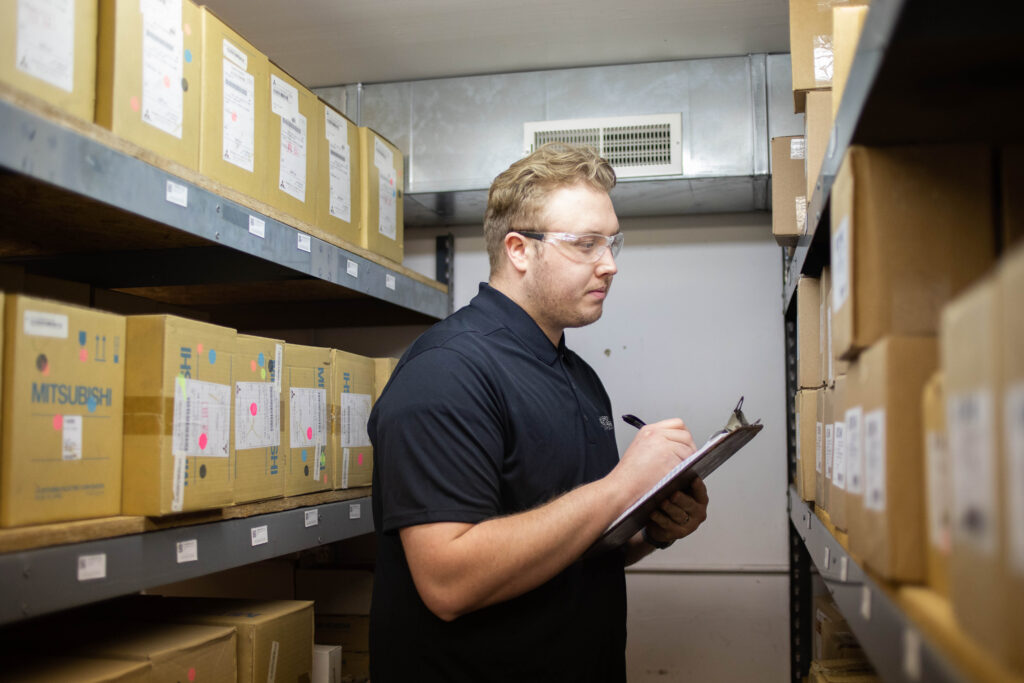
Wherever you store them, the environment needs to be within the manufacturer’s recommended storage conditions, often including a temperature-controlled building that is clean of contaminants like dust, dirt, moisture, and corrosive gases. For equipment like motors, you don’t want it too close to railroad tracks, crushers, or other major vibration sources that could damage the bearings.
You also want a location close to your production facility and easily accessible in case of a failure. It needs to have the ability to be accessed not only at the right time but also by the truck or equipment that will deliver the spare. You also need to be able to offload and reload the items as required, including appropriate cranes, forklifts, and other equipment.
Maintaining spares
For spares to be in working condition, you must have a maintenance plan. For some companies this means simply rotating equipment into service annually during shutdowns, but others may leave spares sitting in storage longer. The manufacturer will also have guidelines for this, but some best practices are universal.
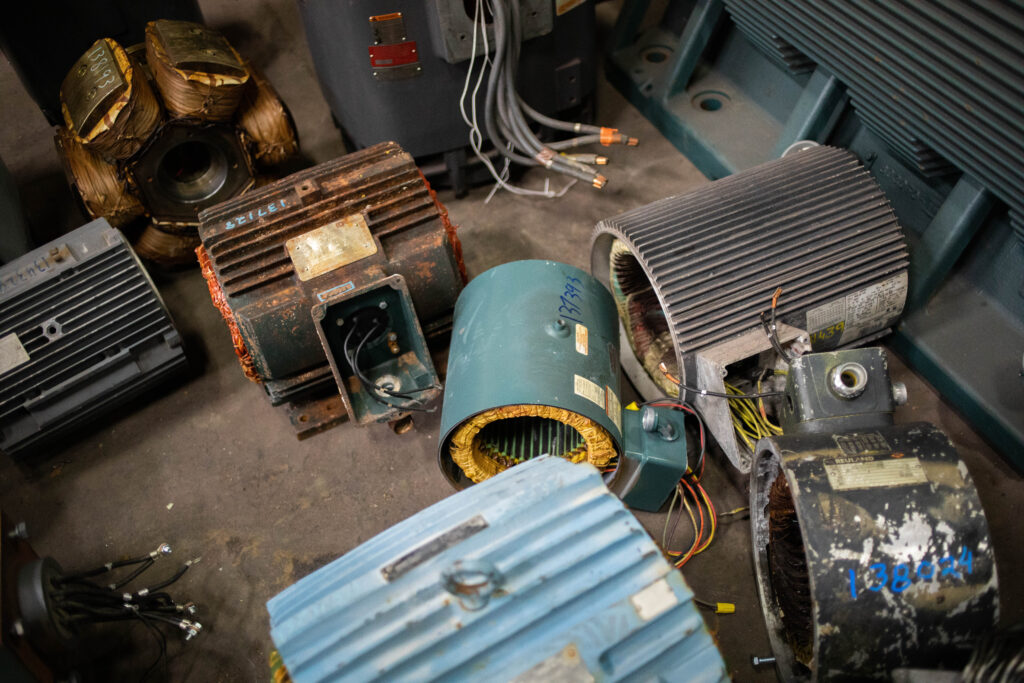
For VFDs, make sure you are cleaning and testing them, as well as reforming electrolytic capacitors. For motors, make sure you’re turning the shafts and performing testing. For generators, ensure that oil changes, fluid checks, and other preventative maintenance are happening as needed. If you need help maintaining your equipment, reach out to our team.
Managing inventory and assets
Even worse than not having a spare at all could be thinking you have one available when you don’t. You could spend time driving to a storage site, searching a warehouse, and losing hours or days trying to locate a spare previously used on another application.
No matter what system your company uses, make sure that you have a way to track spares on order, on site, and when they have been used. Verify the stock as frequently as needed and make sure that information is accessible in the case of a failure.
Monitoring and reporting on usage
When you have spares and track the usage, you can begin to improve your critical spare plan. As you start going through spares, you can see what you use and what you don’t. You may find your original plan was slightly off and needs readjustment. You may also start to identify areas of common failures or pain points you didn’t initially notice.
If you notice a spare is not getting used, that doesn’t necessarily mean that you were initially wrong. Before adjusting your plan, make sure you go back and identify why somebody originally ordered the spare. It may not be a common failure, but could be critical to your processes and worth having a spare even if failure is unlikely.
Let us help you plan
Developing a plan, evaluating your system, sourcing spares, and storing the spares can seem like a lot to manage. For many of our customers, we’ve been able to help with this process. We can help with every step of the process, including storing and maintaining them at our facilities when it makes sense.
If you have questions or want help with your critical spare plan, reach out and let one of our experts help you.
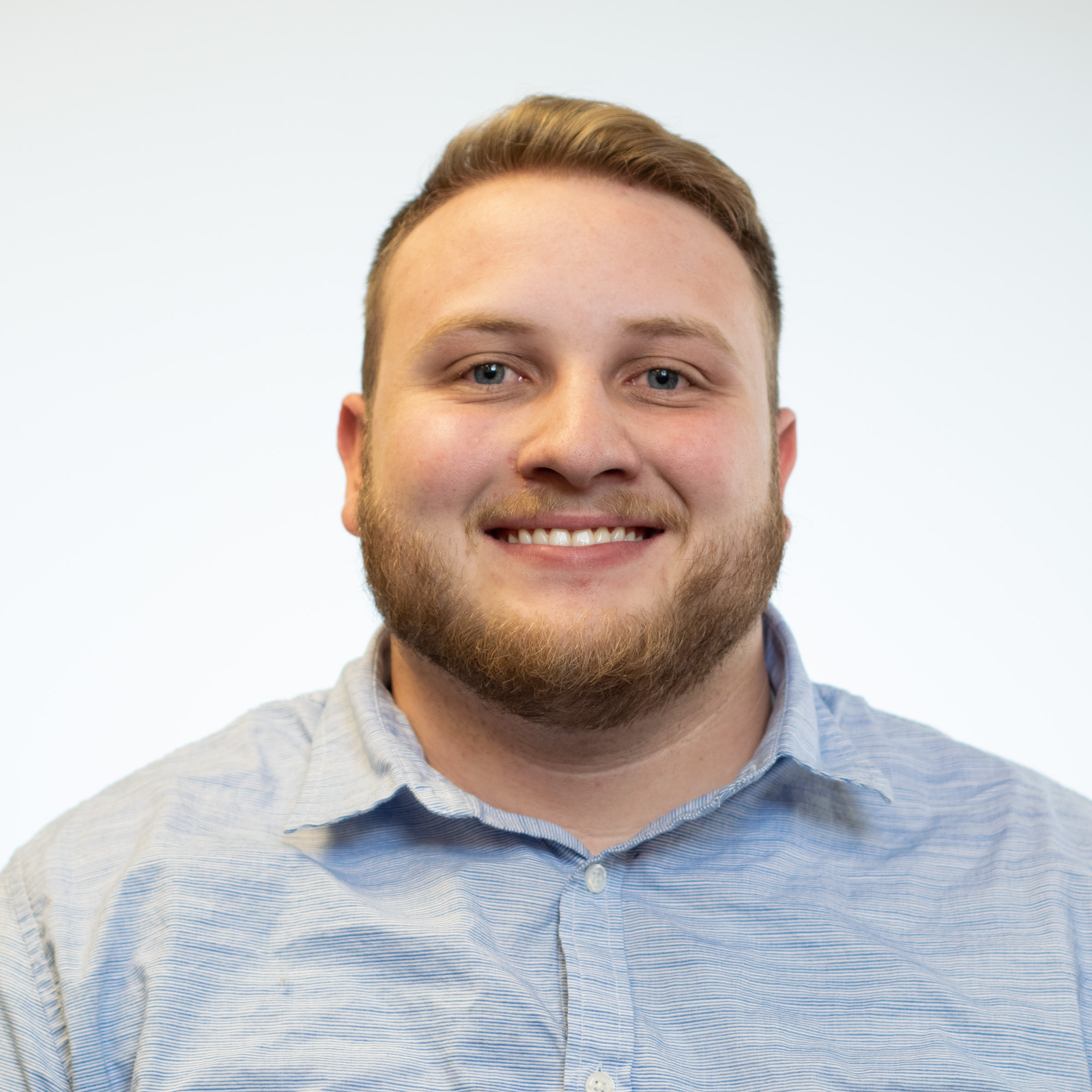
Marketing Manager
Tyler is a marketing manager focusing on VFD, motor, and generator applications. In the past he’s worked in sales for these same products. He is a proud graduate of Utah State University and enjoys spending time with family and friends.