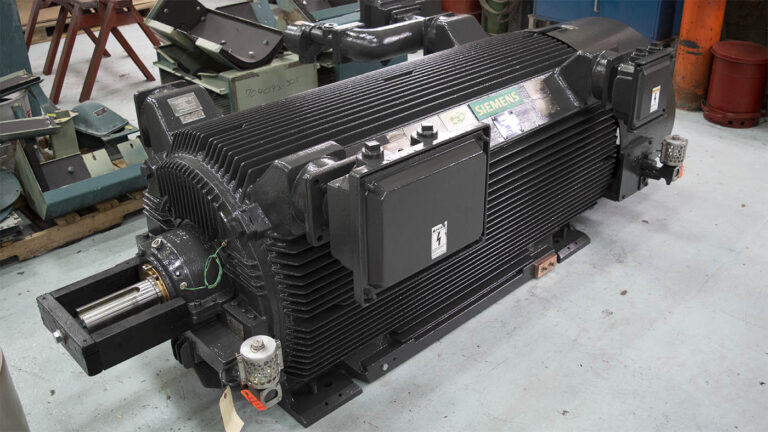
What is Vibrational Analysis?
Changes in the vibration patterns of your motor are one of the first indicators that your motor may be heading toward a critical failure. Vibration analysis experts estimate that by the time your motor starts making audible noise, your motor is only 1-4 weeks away from a critical failure, whereas a slight change in vibration patterns, invisible to the naked eye or ear, starts about 1-9 months before the same critical failure would occur. These early issues are hard to catch and correct without using vibration analysis as a predictive maintenance tool.
Vibration analysis includes the measurement of movement on any given point on a machine and the analysis of those movement patterns. Sensors are used to transform mechanical motion into an electrical voltage. The electric signal is then sent to a vibration analyzer and studied by a technician to see what issues may be starting to arise in your equipment. These measurements are used to identify many different problems, including imbalance, bearing failure, mechanical looseness, wear, misalignment, electric motor faults, bent shafts, gearbox failures, empty space in pumps, and critical speeds.
What are the Benefits?
There are many benefits to vibration monitoring and analysis, including failure predictability, safety, increased revenue, and peace of mind. Increased failure predictability allows maintenance staff to schedule needed repairs when downtime will least affect the plant or business. Safety is improved by taking faulty equipment offline before hazardous conditions occur. Revenue is positively impacted by having fewer unexpected failures. This helps to prevent a halt in production and cutting into the bottom line. Also, peace of mind is increased by building confidence in maintenance schedules, budgeting, and productivity estimates.
What Does Vibration Analysis Measure?
Acceleration, displacement, and velocity are all parameters that are measured when performing vibration analysis.
Acceleration signals place importance on the high frequencies and the change in the speed of the vibration. These signals can then be converted to velocity or displacement.
Displacement signals place importance on the low frequencies. They are usually only used when looking at the broad picture of mechanical vibrations. You can use displacement to find unbalance in rotating parts.
Velocity is related to the destructive forces of vibration or the speed of the vibration, making it the most important parameter. It places equal importance on both low and high frequencies. The root-mean-square (RMS) value of velocity shows vibration severity the best. (RMS is calculated by multiplying peak amplitude by 0.707.)
Amplitude and frequency are two other areas of measurement. Amplitude indicates the severity of the problem, and the frequency will help to identify the source of the problem.
When is Vibration a Problem?
Once the vibration is measured and all data is gathered, it is time to interpret that data. There are many different principles, forms, and categories of vibration analysis that will give you information on each individual part of your machine, but if you want a very simple baseline to start with, take measurements of the vibration of your motor on 2-3 axes and compare the values measured with the values found in the table below.
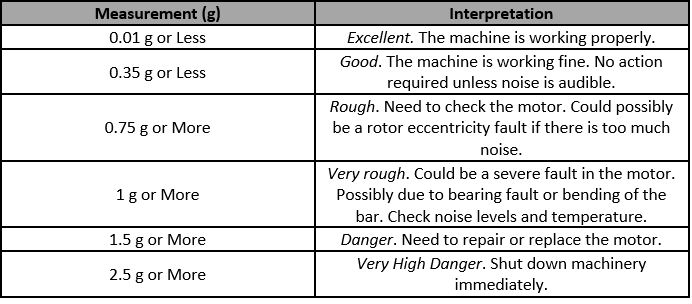
Got More Motor Questions? We Can Help!
Call 800-595-5315 Or Connect With Our Expert Technicians Here:
Other Articles
- How to Reduce Motor Downtime and Keep Your Motor Happy
- Critical Spare Planning
- The Three Most Common Externally Caused Motor Failures
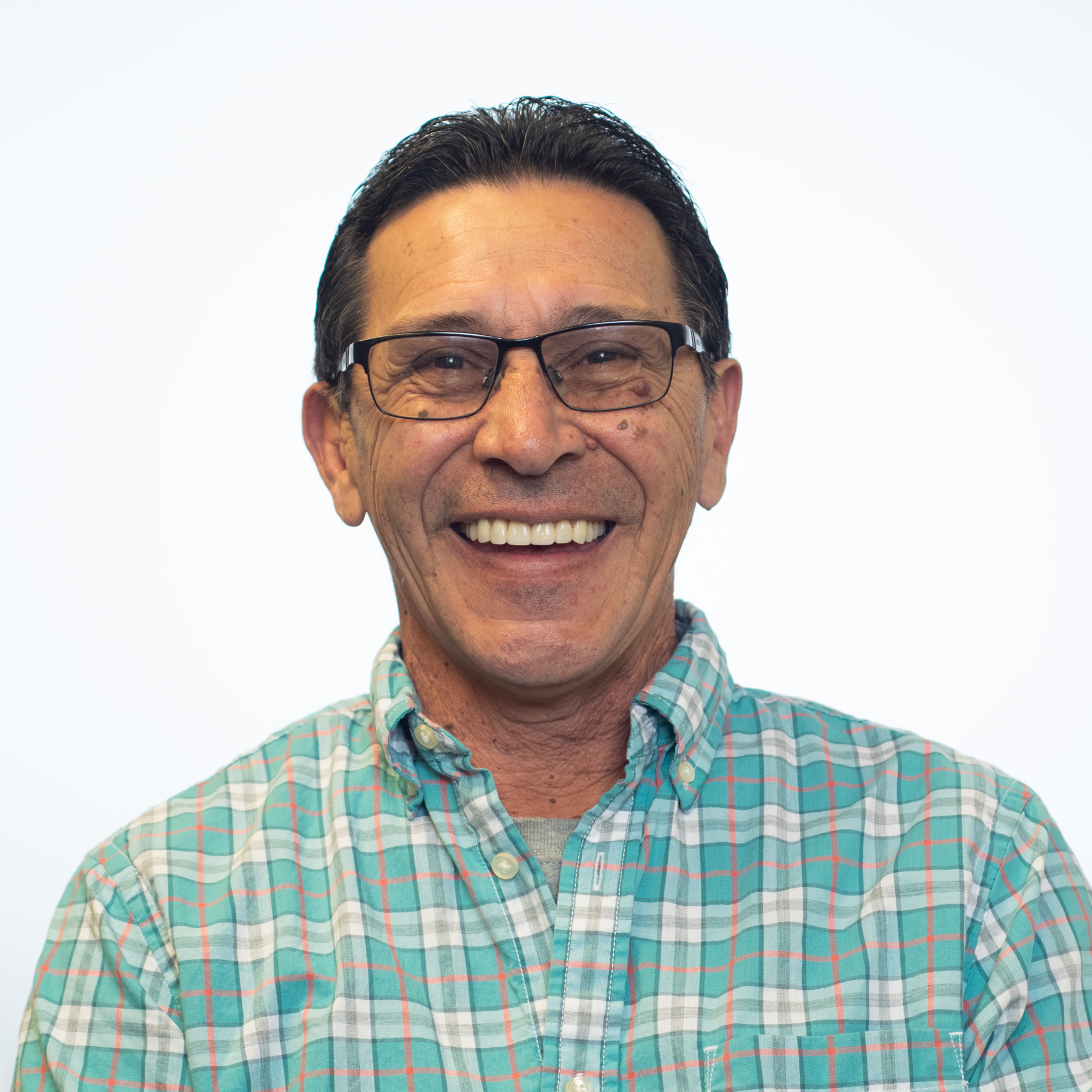
Gary has 30+ years of experience at Energy Management Corporation working in all aspects of motor and mechanical repairs. In his extensive career, some of the interesting projects he has worked on include Hoover Dam hydro generators, Utah power sub stations, harmonic filters for VFDs, and motor for the Buckeye Bullet that set the land speed record for electric car.