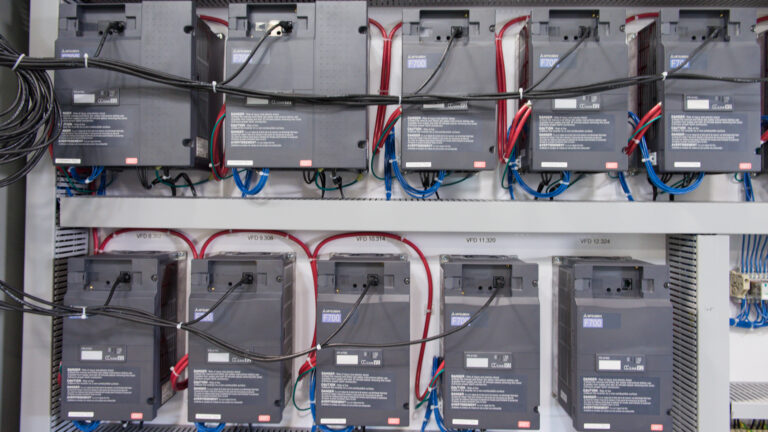
The Origin of VFDs
Variable frequency drives (VFDs) are carefully designed energy saving devices that can pack a big punch, both in terms of conservation of energy and conservation of funds. These devices came into popularity during the 1970s when an energy crisis forced American businesses to look for creative ways to conserve both energy and capital in order to stay afloat.
What Does It Do?
VFDs allow for more precise control over the speed of AC induction motors. AC induction motors are used in a variety of applications such as pumps, blowers, fans, elevators, and HVAC units. The speed and torque of an AC induction motor is directly proportional to the frequency and voltage of its power supply. Most electricity comes into your building at a fixed frequency and voltage (120V and 60Hz in America) from the utility, which means that the motors in your facility are run at a constant speed and torque, even though their actual load may require much less power.
How Does It Do It?
VFDs work, in the most simplified explanation, by intercepting incoming electricity from the utility and modifying it using Pulse Width Modulation (PWM) to meet, but not exceed, the load requirements for your application. This means that VFDs can run motors at different speed and torque as your application’s power needs change. VFDs are best utilized in applications with variable torque loads, which may not always need to run full bore because their load tends to fluctuate from moment to moment. Motors that do not run full bore for the entirety of their lifetime will have less wear, have less critical failures, and use less energy than motors that run at full power all of the time.
Most motor manufacturers recommend installing an oversized motor in order to deal with your facility’s “worst case scenario peak loads”. However, peak load parameters are hardly ever met by most facilities on a day to day basis. This means without a VFD, your motor may be consuming much more energy than needed most of the time. This results in wasted energy and wasted money on utility payments, repairs, and equipment replacement due to overuse. Using a VFD can allow you to use your motors at much lower energy consumption levels until peak load scenarios actually come into play. Once peak levels are reached, the VFD can then speed up the motors to deal with those higher energy needs, but only for as long as the need is present.
What Is The Catch?
Unfortunately, like anything, VFDs don’t come without their faults. VFDs create harmonics, which are strictly monitored by utilities in accordance with IEEE 519. This means that in addition to the cost VFDs add to your application, you will also need to invest in some form of harmonic mitigation technique; such as passive harmonic filters, a higher pulse VFD, or an active harmonic filter to avoid being penalized by your utility power supplier.
Summary
To recap, VFDs work well in applications with variable loads. Common examples could be an HVAC unit in a large building, cooling pumps, water pumps, fans, blowers, injection molding machines, elevators, conveyor systems, etc. VFDs will save energy, reduce unnecessary wear on your equipment, offset oversizing, reduce demand charges, and even help you with your bottom line. Financial incentives such as tax deductions, rebates, or even utility credits are available to most businesses that utilize these energy saving devices in their day to day operations.
For additional information, check out our EMC Webinars on VFDs
Got More VFD Questions? We Can Help!
Call 800-595-5315 Or Connect With Our Expert Technicians Here:
Other Articles
- What is Right for Your System – Deraggers or VFDs?
- Convention Center Saves 8% in Energy Usage
- Local University Uses EMC VFDs to Keep Facilities Running
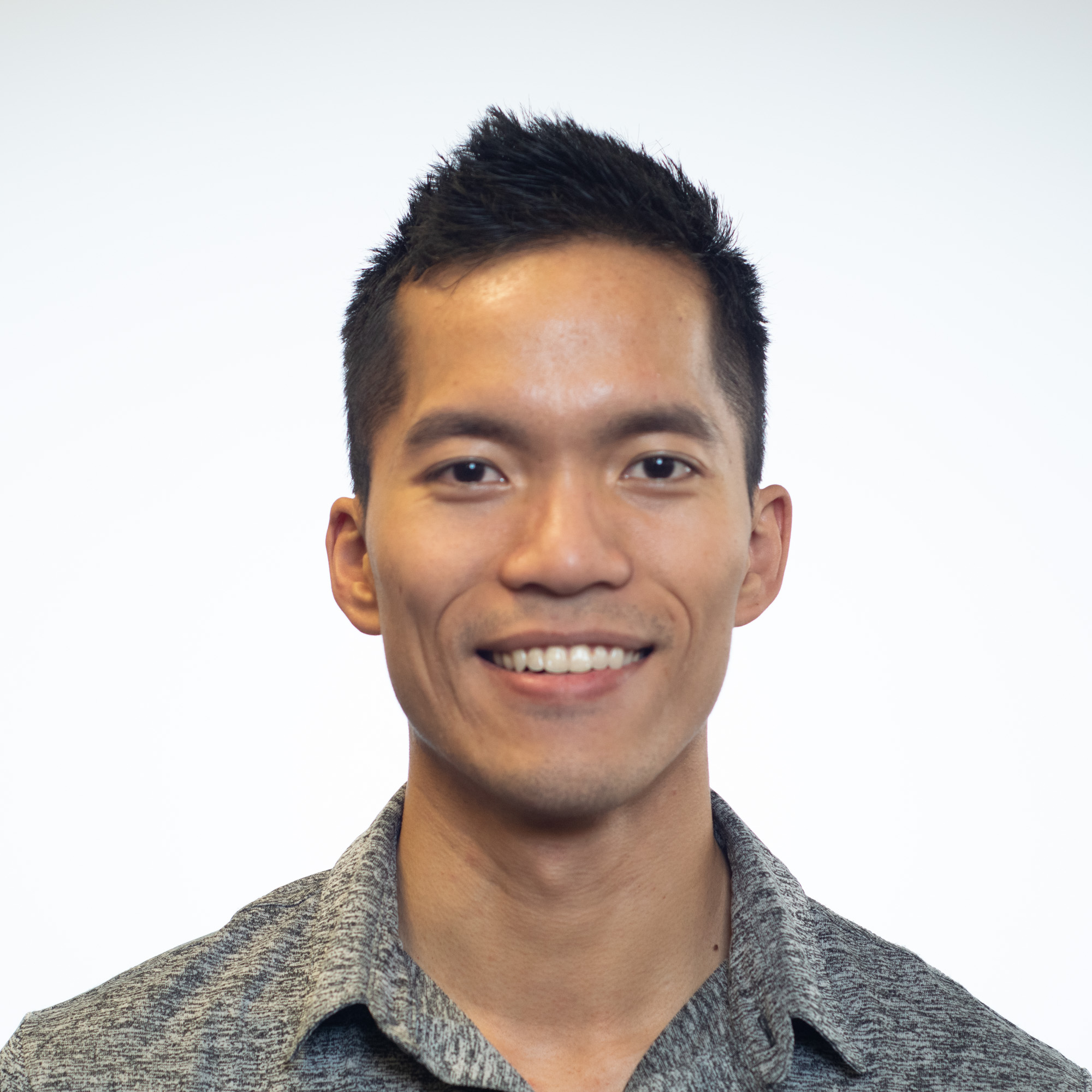
Yin is a content producer and visual designer at Energy Management Corp. He has over a decade of graphic design, photography, and business experiences. Yin specializes in producing written & video content and he maintains the visual branding of EMC.