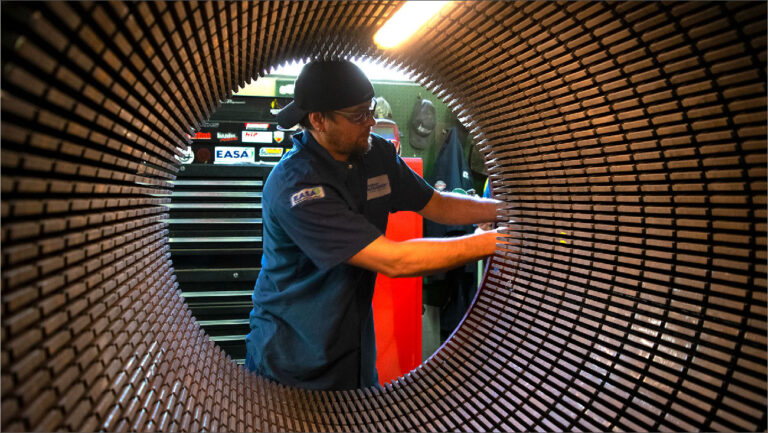
Is Your Motor Showing Early Warning Signs?
Motors need to be dependable but if you don’t maintain your motor, you could suffer motor failure. Motors can be expensive to repair and if motors fail it could be a huge loss.
Recognizing your motor’s early warning signs can keep your motor running well and possibly save your motor from failure.
Have you experienced any excessive vibration, unusual or excessive noise, areas of burnt paint, dirty housing openings, smell of burning, signs of corrosion, signs of excessive wear, a bearing housing that’s hot to the touch, oil and grease leaking from your bearings, or loosening connections? These are warning signs that motor failure may be on your horizon.
Knowing the causes and solutions to common motor problems can be the difference between a working motor or a motor failure so bad that it requires serious repairs or replacement.
Some of the causes of motor failure are hard to detect, or can go unnoticed until it is too late. Awareness at the beginning is important and can save you lots of money on future repairs. This article is the beginning of a series of articles about common motor failures. Click the links below to read more about common motor failure problems, in order from most common to least common:
1. Bearing failure
2. Stator winding
3. External conditions
4. Rotor bar
5. Shaft Coupling
Five Most Common Causes of Motor Failure
1. Bearing Failure (51%)
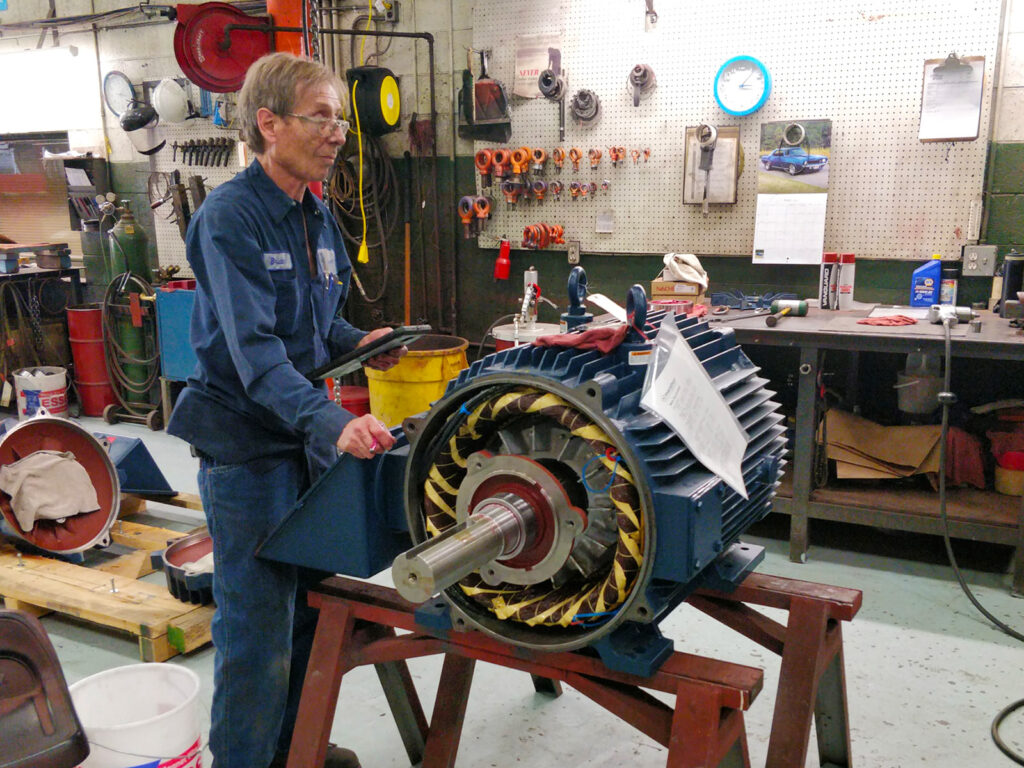
- Insufficient: Re-greaseable bearings need regular maintenance. Most manufacturers recommend re-greasing your motor bearings after every 2000 hours of operation or every three months, whichever comes first. Check with your motor manufacturer for their recommendations on lubricating intervals.
- Excessive Greasing: Excessive greasing can lead to excessive overheating of your bearings which in turn can lead to bearing failure. To ensure that you are not over-greasing your equipment, check that grease relief valves are open during the re-greasing process, make sure that all relief valves are clear of any dirt or hardened grease, remove the grease outlet plug or open outlet valve where fitted, and slowly pump the grease into the bearing. (Grease guns are capable of producing excess PSI and adding the grease slowly can help mitigate this.) Discontinue greasing if any abnormal back pressure is felt.
- Wrong Lubricant: Different types of grease are incompatible with each other due to their chemical makeups. Use only the manufacturer recommended type of grease to avoid any grease incompatibility issues.
- Misalignment: It is essential that your motor and load be correctly aligned under actual operating temperatures and conditions. Machines that are correctly aligned at room temperature may become badly misaligned due to deformation associated with temperature change when in operation. Misalignment should be checked approximately every 2,000 hours of runtime. Both the operating and non-operating alignment should be checked every time you reach this interval.
- Shaft Overload: Excessive loading through the shaft of your motor may contribute heavily to motor failure. Belt driven pulleys often put high loads directly onto the shaft bearing. One way to monitor shaft overload is to keep track of how often your belts are bottoming out – if it is happening more than reasonable – shaft overload is likely the cause.
- Vibration: Excessive motor vibration can be a contributing factor to the failure of many different motor components. Make sure to check that motor mounting bolts are secure, as vibration may cause them to become loose during operation. In order to tell if your vibrational levels are normal, refer to the vibration severity tolerances set out by ISO 10816.
- Overheating: Before selecting a motor, be sure it is designed to cope with the heat it may be subjected to. Bearings come in a variety of clearances to allow for thermal expansion in operation. For every 15o C cooler you can keep your motor than normal operating temperature, you can double the re-greasing interval/life of your bearings.
2. Stator Winding (16%)
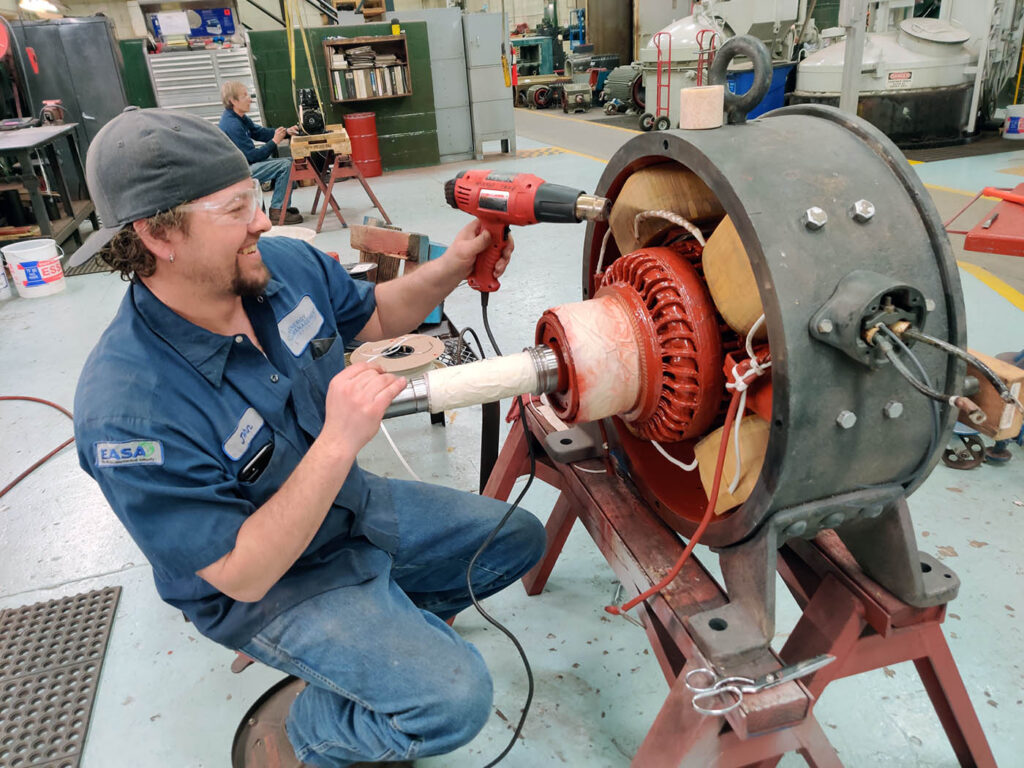
Winding failure only accounts for 16% of reported motor failures. Winding failure can occur for a few reasons including:
- Overloading: Motor windings can begin to fail due to overloading at the motor shaft which causes excessive heat build-up and eventually motor failure. A thermal overload relay is a common method used to protect against overload.·
- Overheating: The cooler your motor operates, the longer its expected operating life is. Excessive starts are a major cause of overheating. During start up, a motor typically sees between 6 to 8 times its rated current. This can increase the thermal status of the motor, increasing thermal stress on the windings and contributing to motor failure. One way you can tell if your windings are under stress is to look for darkened areas on the motor windings – these marks are usually signs of overheating.
3. External Conditions (16%)
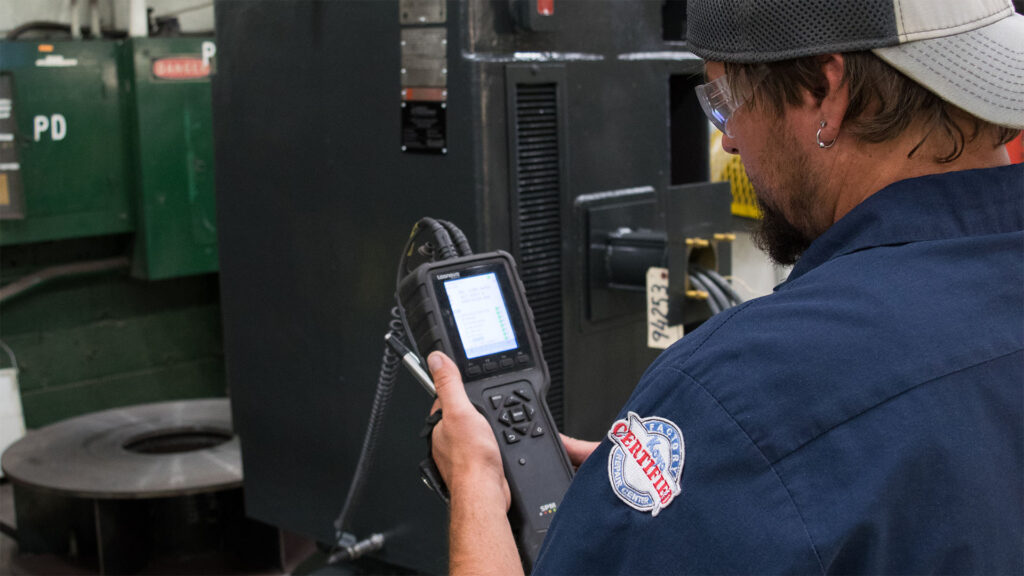
External conditions contribute heavily to 16% of reported motor failures. External conditions that could ruin your motor include:
- Heat (Motor Operating Temperature): Insulation systems offering high levels of protection against heat are a great idea to prevent against motor failure. Always be sure to maintain your motors cooling system. Broken fans, clogged vents, or blocked or damaged cooling fins can cause excessive heat buildup causing quick degradation of internal wiring insulation.
- Humidity: Electricity and water are a bad mix. High humidity can allow moisture to enter the motor and cause damage and corrosion. Humidity can be combatted by opening drain hole plugs, fitting anti-condensation heaters, and utilizing additional corrosion protection (i.e. enhanced paint systems or coatings). If you cannot completely seal against moisture ingress, ensure that the breather plugs are fitted and kept clear – this will ensure that all moisture that enters can drain away.
- Contamination: Any foreign particles that find their way into the motor enclosure can cause irreparable damage, particularly to motor bearings and windings. Do everything humanly possible to keep any contamination particles away from your motor to preserve its longevity.
- Heat (Ambient Temperature): Before purchasing a motor, be sure that it is rated correctly for the ambient condition in which it will operate. Derating is often necessary for high ambient temperatures whilst extremely low ambient temperatures may require specialized insulating materials.
4. Rotor Bar (5%)
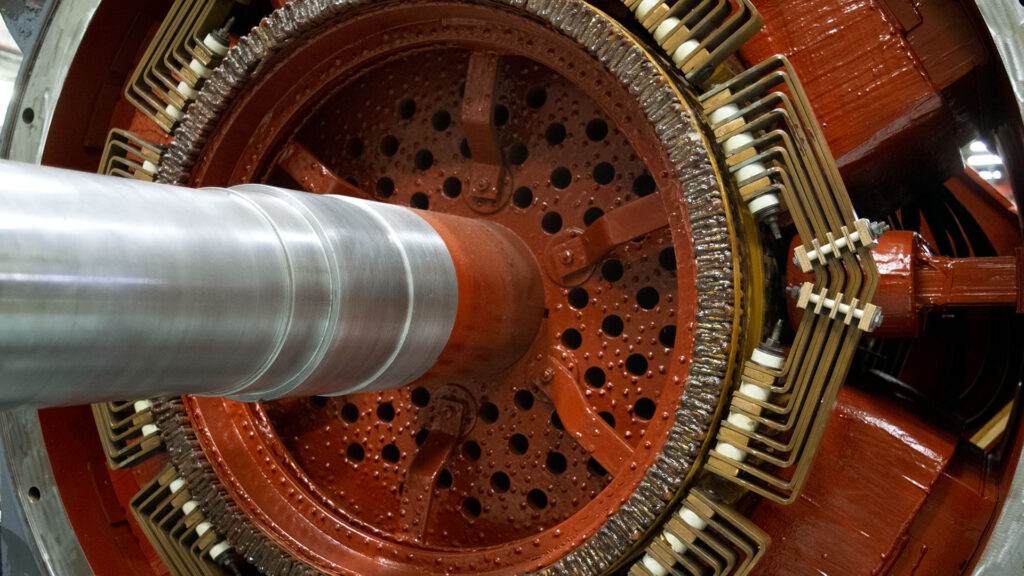
Rotor bar issues contribute to 5% of all reported motor failures. Below we will discuss three ways rotor bar problems can contribute to motor failure:
- Starting Frequency: Heating, cooling, acceleration, and deceleration can cause thermal stress and inertia fractures. Starting time is a function of load torque, inertia, and motor torque. As the starting current is always very much higher than the rated current, an excessively long starting period will cause a harmful temperature rise in the motor.
- Overloads: In a locked rotor or stalled condition the rotor can experience sudden and excessive temperature rise that can cause the rotor cage to fail. Sudden increases in temperature often occur during start-up. Motors can stall during normal operations due to mechanical faults including seized bearings, heavy loading, or possible foreign objects caught in the motor could be possible causes.
- Under Voltage: Under voltage increases running current, causing overheating and a reduction in efficiency – eventually leading to failure.
5. Shaft Coupling (2%)

Shaft coupling problems only account for 2% of reported motor failure. Misalignment and bad installation are two ways shaft coupling issues contribute to motor failure:
- Misalignment: A coupling that is badly aligned suffers some unusual load stresses that can lead to motor failure. Ensure that your coupling is aligned parallel to the shafts.
- There are three types of misalignment:
- Mechanical: Experience has shown us that any motor and motor driven load may twist out of alignment during shipping or moving. Proper alignment of direct-coupled drives can be accomplished by a dial-indicator, laser, or computerized instrumentation.
- Parallel: This is the offset between the centerlines of the two shafts. This can be determined by mounting a dial indicator on one coupling half with the indicator probe bearing radially on the other coupling half, and then rotating both shafts together through 360 degrees.
- Angular: This is the amount by which the faces of the two coupling halves are out of parallel. This may be determined by mounting a dial indicator on one coupling half with the indicator probe on the face of the other half, and then rotating both shafts together through 360 degrees to determine any variation in reading. During this check, you must keep the shaft of a motor with endplay against its thrust shoulder to prevent false readings due to shaft movements in the axial direction.
- There are three types of misalignment:
- Bad Installation: The biggest cause of coupling failure is due to incorrect mounting. Make sure to research and use the appropriate fitting techniques for your specific motor. There are two main couplings available:
- Rigid: For use when shafts are coaxially aligned.
- Flexible or Compensating: For use when shaft alignment cannot be guaranteed or there is expected distortion or movement that could be transmitted through the shaft.
How to Prevent Motor Failure
When installing a new motor, be sure to document the operating condition, machine specifications, and performance tolerance ranges. Make sure to document critical measurements at installation, before and after maintenance and on a routine basis. It is a good idea to create an archive reference of measurements to facilitate trend analysis and identify any change of state or conditions. One way to keep track of your stats is by plotting individual measurements to establish a baseline trend. Any change in this trend line of more than +/- 10% – 20% should be investigated to the root cause to understand why this issue may be occurring and solve the problem before it becomes fatal.
Want to learn more?
If you want to learn more about any of the common motor issues, read our article series that expands on each of these common motor problems listed in this article.
- Bearing failure
- Stator winding
- External conditions
- Rotor bar
- Shaft coupling
We Specialize in Troubleshooting and Repair of Electric Motors!
Call 800-595-5315 Or Connect With Our Expert Technicians Here:
Other Articles
- How to Reduce Motor Downtime and Keep Your Motor Happy
- Critical Spare Planning
- The Three Most Common Externally Caused Motor Failures

It really interests me to read such articles, thanks for sharing. Blogs like yours really helps me learn more day by day.
Your blog is a valuable resource. I appreciate the quality and variety of topics you cover. Looking forward to more!